Seismic Module
The Seismic module addresses the needs of the seismic Industry for the accurate planning, installation, and retrieval of Ocean Bottom Cables (OBC) in mid- and deep waters. OBCs often have transponders along their length, which can provide accurate position measurements at points along the cable. By inputting data from these transponders, the accuracy of Makai’s cable model can be significantly improved inturn providing higher placement accuracy of the cable on the sea floor. This is of particular importance for OBC installations where transponders are placed at regular intervals along the arrays.
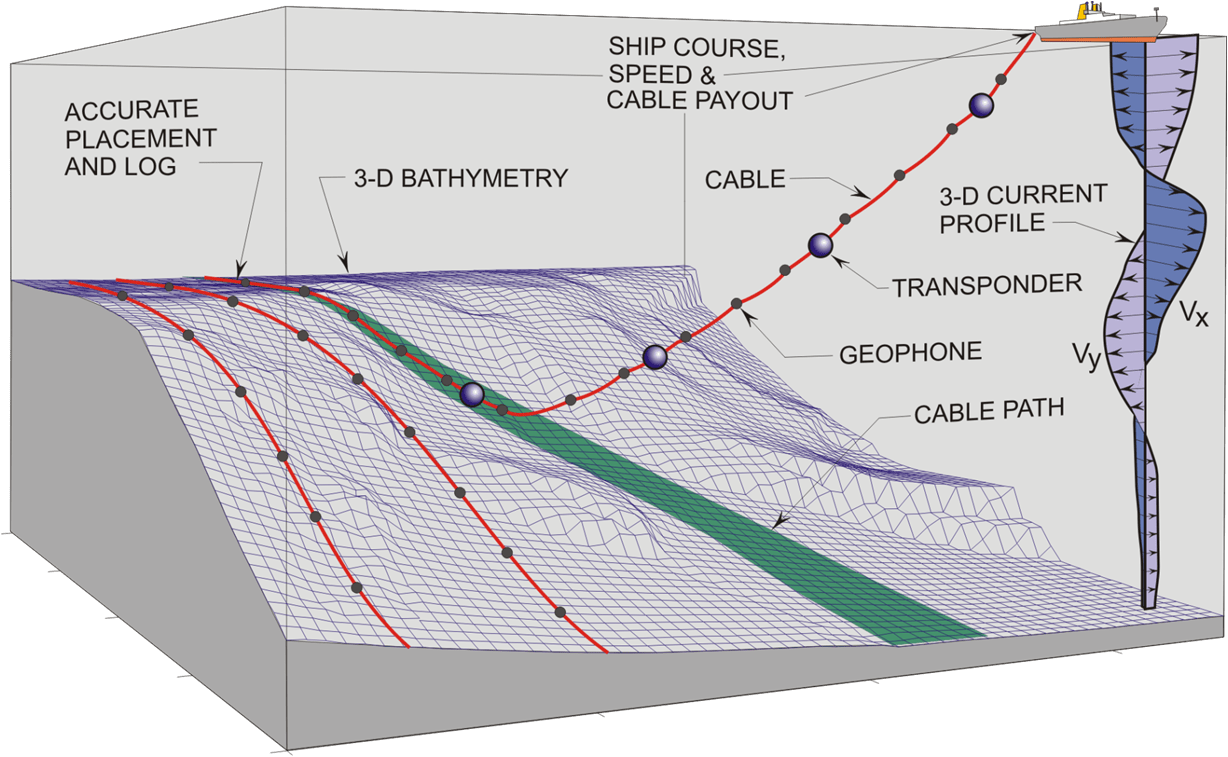
MakaiLay Seismic Cable Software
Installation/Retrieval Planning and Equipment Selection
Installation planning and equipment selection is achieved by running computer simulated cable lays in the office to model the effects of changes in cable type, equipment, procedures and environmental conditions of the lay. Such simulations allows for detailed analysis/selection of the equipment, techniques and data inputs required to safely and reliably lay/retrieve the cable along the planned route. These simulation results help contractors to fully understand the complexities of the operation well before they have to go to sea, and help them to more accurately bid a project. Operators can make all their mistakes in advance on the simulator when they can be easily corrected and before they become costly at-sea disasters. The system can simulate real world problems such as ship navigation errors, variations in ship and cable payout speed, unobserved changes in ocean currents and bathymetry.
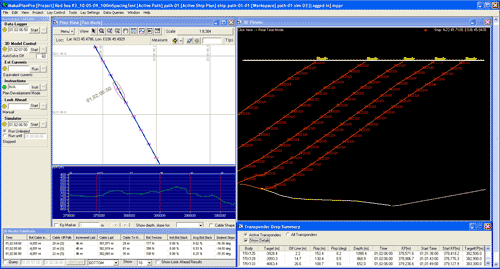
This capability allows users to answer important questions before going to sea, such as:
-
- Is it necessary to measure currents in real time to achieve the desired placement accuracy and tension control?
- Do we need to attach transponders on the cable to achieve desired accuracy and how often?
- What is the fastest speed the cable can be installed and still achieve the desired accuracy in terms of sensor placement and tension control?
- What is the fastest retrieval rate possible without exceeding the maximum cable tension?
- How much can cable dragging on the seabed be minimized by using feedback from transponders attached to the cable and/or by measuring currents during the retrieval operation?
Using Transponders to Improve Placement Accuracy
The control system itself is based on rigorous cable physics, and its accuracy has been validated multiple times in the past. Accuracy is, however, limited by the quality of the input data, in particular the measurements of cable length paid out and ocean currents. Having accurate position measurements of transponders attached to the cable can compensate for some of these input errors and can be used to significantly improve the overall cable and sensor placement accuracy. This is of particular importance for OBC installations where transponders are placed at regular intervals along the arrays.
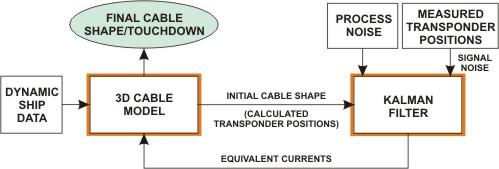
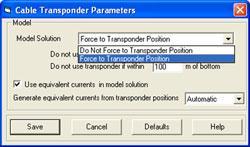
If highly accurate transponder data is available (RMS position error = 0.25% slant range), the control system has the option to directly force the mathematical solution of cable shape to pass through the bottom most transponder position available on the suspended portion of the cable. Since the position of this transponder is known, the bottom transponder effectively acts as a “ship” closer to the bottom, which in turn improves the accuracy of the touchdown location.
If the position information provided by the transponder is not as accurate as desired, the software can still use the positions of multiple transponders in the water column in a Kalman Filter to estimate the ocean currents acting on the cable and improve the cable shape and touchdown computations. This is particularly helpful when ocean currents are not being measured or when the quality of the transponder position data is not very high. The Kalman filter outputs a current profile such that the difference between the measured and calculated (by the model) transponder positions is minimized. These currents can be used by the cable model to predict touchdown conditions in the near future and make corrections to the installation procedure to avoid undesirable touchdown conditions.
Simulating Transponders
In typical OBC installations, transponders are placed at regular intervals along the arrays. Having accurate position measurements of transponders attached to the cable can significantly improve the overall cable and sensor placement accuracy. In the Seismic Module, the transponder data can be utilized by either directly forcing the transponder positions on the cable shape or by passing the measured transponder positions though a Kalman filter to estimate the ocean currents acting on the cable and improve the cable shape and touchdown computations. This is particularly helpful when ocean currents are not being measured or when the quality of the transponder position data is not very high.
MakaiPlan Pro with the Seismic Module can simulate transponder data and then simulate the use of transponders just like they are used in MakaiLay with the Seismic Module. This is possible because MakaiPlan Pro with the Seismic Module runs an additional 3D cable model in the background. For example, if you want simulate how accurately an installation can be made without measuring currents and just relying on transponders, the Seismic Module model will run a simulation in the background with ocean currents incorporated and will generate the transponders positions from the cable shapes of this background model. In the actual simulation, no ocean currents are used and just the transponder data are used. These simulations are helpful in making decisions about the data quality and placement frequency of the transponders.
Interested in Makai’s Submarine Cable Software and Services?
ReACH OUT!
Contact us by sending in this form any time you need professional support or have any questions. You can also fill in the form to leave your comments or feedback for Makai’s team.