Pipelines
Since 1979 Makai has designed a number of bottom mounted, down-the-slope, catenary, and pendant polyethylene pipelines for use in SWAC and outfalls.
These pipelines are suited for:
-
- Seawater Air Conditioning (SWAC)
- Ocean Thermal Energy Conversion (OTEC)
- Marine Outfalls
- Wastewater Treatment
- Aquaculture and Mariculture
- Industrial Cooling and Power:
- Waste heat power cycles
- Power plant cooling
- Liquefied Natural Gas (LNG) process cooling
- Chemical process cooling
- Other industrial processes with large cooling loads
1.4 m (55″) diameter NELHA deep water intake pipeline during assembly.
Pipeline Technologies and Services
Makai’s engineers are experts in large diameter high density polyethylene (HDPE) pipeline design. For decades, Makai has been a world recognized leader in Seawater Air Conditioning (SWAC) and Ocean Thermal Energy Conversion (OTEC), two renewable energy technologies that use deep seawater as a renewable energy resource.
Makai’s Pipeline Expertise
Makai’s long experience with pipeline design and deployment has led to very cost-effective fabrication and deployment methods. One example is a typical SWAC polyethylene pipeline, which is fused into long sections onshore, filled with air, then towed into place and lowered to the seabed – often in a single day – minimizing expensive marine construction and weather-related risks.
Makai has also conducted extensive field research on practical and cost-effective methods of deploying large diameter pipelines – in both deep and shallow waters. In order to ensure the safety or our designs, Makai has developed special test equipment and procedures for testing polyethylene pipes under extreme loads and under negative (suction) pressure. Makai has been designing and working with deep water pipelines since 1979 and has designed a number of down-the-slope polyethylene intake pipelines and suspended pipelines.
Numerous firms place pipelines on the ocean floor – usually at great expense. Makai’s design services lead to reduced cost by assembling the pipe onshore where labor costs are lower. The assembled floating pipe is towed into place and mounted to the seabed – often in a single day – minimizing expensive marine construction and weather-related risks.
Installing these unique deep pipes can place substantial loads on the pipe assembly during installation. Makai conducts field research studying the installation and loading on large diameter pipelines – both deep and shallow. Makai also develops and tests the procedures needed to accommodate these loads. Here, a 1:5 scale model of a 55″ pipe and custom flange assembly is measured while it is pressurized, tensioned and severely bent.
Installed Pipelines
Makai’s experience in pipeline design, analysis and deployment is summarized below:
Al-Jubail SWRO Desalination Plant
In 2021 Makai designed the deployment method for structured pipelines (2.9 m intake and 2.8 m outfall) of the Al-Jubail SWRO Desalination Plant in Saudi Arabia.
More Info
These pipelines supply and discharge seawater to and from the world’s largest desalination plant and are the largest pipelines that Makai has helped install.
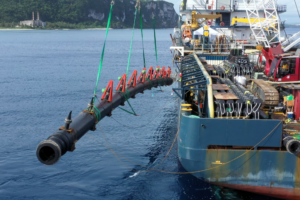
Guam Outfall Diffuser Deployment
Makai developed the deployment plan for an outfall diffuser in Guam, that was recently installed by our Client and prime contractor, Healy Tibbitts Builders (HTB).
More Info
The project added a diffuser section to the existing outfall pipe for the Guam Waterworks Authority treatment plant.
As part of this project, Makai simulated the deployment of this system in approximately 150 ft water depth. From the simulation results, we worked closely with the contractor to develop the methods to safely deploy the system. The deployment team was successful in installing the diffuser section, and the outfall is fully operational.
See a video covering the deployment of this system here.
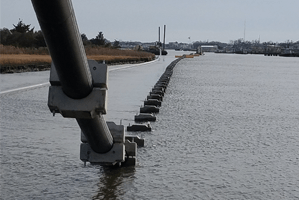
Rehoboth Beach Outfall
In 2018 Makai provided HDPE pipeline deployment analysis for the 24-in. diameter, 11,400-ft.-long pipe leading from the wastewater treatment plant to the Atlantic Ocean.
More Info
In Delaware, a $52.5 million project to eliminate the discharge of treated effluent from the Rehoboth Beach into the Lewes-Rehoboth Canal has been designed and installed. Part of this project involves installation of the force main pipe which is a 24-in., 11,400-ft.-long pipe leading from the wastewater treatment plant to the Atlantic Ocean. It travels approximately 6,000 ft. off the beach before diffusing treated wastewater into the ocean. The HDPE pipeline is horizontal direction drilled approximately 3,000 ft. followed by marine open-cut trench approximately 3,000 ft. Once the pipe is anchored in place with concrete collars, the open-cut trench is backfilled. The terminus of the outfall pipe consists of a 120-linear ft. diffuser comprised of eight risers, 1.5 ft. above the ocean floor, with four discharge ports per riser. Makai assisted Manson Construction by providing HDPE pipeline deployment analysis (pull forces, stresses, flooding rates required), ballast weighting schedule, design of precast concrete ballast weights, investigating anchoring methods, reviewing HDPE pipe pull head and towing assembly, and investigating pipe fabrication staging sites. Outfall pipeline installation is ongoing as of March 2018.

Burullus Power Plant Intakes
Makai completed the final design and construction support for the twin 2 m diameter, 1.2 km long HDPE intake pipelines and twin intake towers for the new Burullus power plant in Egypt.
More Info
Makai worked directly for the marine contractor, Tideway (DEME), to provide final designs and installation guidance. This seawater supply system is designed to serve what will be one of the world’s largest natural gas-fired power plants. Design of the intake structures was driven by their shallow depth (5 meters) and the fact that breaking waves were present in the area. Makai was responsible for HDPE pipeline and installation specifications, intake system hydraulics including computational fluid dynamics analysis, intake tower and anchoring concrete structural designs and specifications, and contractor support during installation including design of lifting and staging assemblies.
Cayuga Power Plant – Cooling Water Intake System
Makai completed the final design of a cooling water intake system for a large power plant in Upstate New York. Final construction, installation and commissioning was completed in January 2017, and the system is now fully operational and supplying 170,000 gallons per minute (~10.7 cubic meters per second) of cooling water to a power plant.
More Info
The Client is one of the nation’s first large utility plants to go through the EPA Clean Water Act, Section 316(b) process in its entirety. Screens were fine slotted mechanically cleaned cylindrical wedge-wire screens supplied by Intake Screens Incorporated (ISI). Makai used an integrated design approach, optimizing the structure through a continuous iteration of CFD (computational fluid dynamics), FEA (finite element analysis), and value engineering on the structural arrangement for constructability, fabrication, and shipping. Our team delivered a custom solution for the client that meets their strict hydraulic limitations, their budget, as well as the stringent EPA 316b guidelines that will help to preserve the marine ecosystem.
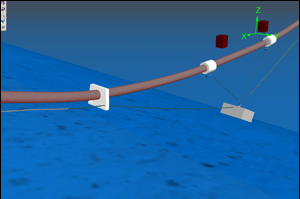
Hawaii – 1 m Pipe Repair
In 2011, Makai performed final design and construction oversight for the repair of a deepwater 40” (1.0 m) diameter HDPE pipe at the Natural Energy Laboratory of Hawaii (NELHA).
More Info
The pipe, originally built for ten year design life, has been in place for over 25 years. The pipe design involves a 915m long floating catenary section from 150m to 670m depth, and several of the chain bridles restraining the pipe had worn from corrosion and continuous motion over the years. Makai simulated the current pipe conditions using Orcaflex 3-dimensional finite element software, simulated repair solutions, and provided final design drawings and specifications. In July 2013, repairs were conducted and Makai provided on-site representation for our client, the State of Hawaii. The repairs were successful, and post-repair measurements showed excellent agreement with Makai’s model predictions and design specifications.
Lake Oswego Sewer Interceptor
In 2011, Makai modeled and performed analysis for a 42-inch HDPE submerged, buoyant sewer interceptor. Makai used OrcaFlex to model the tension and stresses to a very high degree of precision.
More Info
The Lake Oswego Interceptor Sewer (LOIS) project, protects the water quality of Oregon’s Oswego Lake through seasonal changes in water temperature and in the event of an earthquake. The project replaced a 50-year-old corroded, undersized, and seismically vulnerable concrete cylinder sewer pipe under the lake with a larger, flexible, high-density polyethylene (HDPE) pipeline. LOIS is the first known buoyant gravity sewer in the world. LOIS’ submerged, buoyant stainless-steel access points provide entry points to the pipeline without affecting boat navigation, and the installation of removable access caissons allows cleaning and inspection equipment to be inserted into for infrequently required maintenance. Makai modeled and performed analysis for a 42-inch HDPE submerged, buoyant sewer interceptor. Makai used OrcaFlex to model the tension and stresses in hundreds of components (especially the tethers) to a very high degree of precision; the grade tolerance on the project was plus or minus ½ inch over several miles. Makai performed this work for Lake Oswego, Oregon and Brown and Caldwell Engineering. The project won two national awards. The Plastic Pipe Institute declared the Lake Oswego Sewer Interceptor Project as its Municipal Project of the Year, and the Association of General Contractors awarded their 2011 Grand Award to Advanced American Construction, Inc. for their work assembling the project.
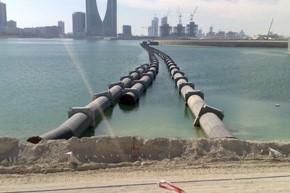
Bahrain District Cooling
In 2005, Makai designed intake and discharge pipelines to provide seawater to the Bahrain Diplomatic Area District Cooling Project’s air conditioning plant for condenser cooling.
More Info
Seawater drawn from the Arabian Gulf is slightly warmed and then returned into near shore waters. The system, owned by Tabreed Bahrain, features a 63” (1.6 meter) diameter by 2240’ (683 meter) long intake pipeline, and a 55” (1.4 meter) diameter by 5104’ (1556 meter) long outfall pipeline with a 20 port diffuser, operating at a flow rate of 60,000 gallons per minute (3.79 m3/sec).
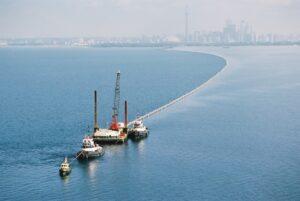
Toronto District Cooling
In 2003, Makai performed significant design aspects for the three deep water intakes for ENWAVE’s Deep Lake Water Cooling Project in Lake Ontario. Each HDPE pipeline is 5 km long and 1.6 m in diameter.
More Info
The deep (115 meter) intakes provide cold water for air-conditioning buildings in downtown Toronto and the municipal drinking water system with a maximum capacity of 58,000 tons. The system provides water of higher purity than is provided by the current intakes that obtain water from shallower depths. Each HDPE pipeline is five km long and 1.6m (63″) in diameter. The pipelines were installed during the summer of 2003.
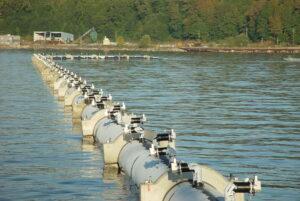
Everett, WA Outfall
in 2003 Makai designed the deep water portion of a 1.6 m diameter outfall pipeline for Kimberly-Clark Paper Company and the City of Everett, Washington. This pipeline goes to a depth of 107 m in Puget Sound.
More Info
This pipeline delivered 70 MGD of treated municipal and industrial wastewater to a depth of 350 feet (107m) in Puget Sound. The total length of the deep water outfall was 2741’ (836m) and included a 1550’ (472m) diffuser section with 80 ports. The alignment included a 40 degree bend right at toe of a steep submarine slope. Makai devised a unique diffuser port plug design that allowed this outfall to be installed using standard controlled submergence techniques for deep water HDPE pipes, and then allowed the diffuser ports to be quickly opened using an inexpensive remotely operated vehicle. The pipeline was installed in late 2003 and has been in service since the spring of 2004.
HOST Park Deep Seawater Pipeline
In 2001, Makai engineered the main seawater supply source for the Hawaii Ocean Science Technology Park (HOST Park). This included a cold-water pipeline 55″ diameter, 3000′ deep, and two miles long.
More Info
Makai has engineered the main seawater supply source for the Hawaii Ocean Science Technology Park (HOST Park) at Keahole Point, Hawaii. This supply system consists of a cold-water pipeline (55″ diameter, 3000′ deep, and two miles long), a 55″ diameter warm water intake pipe, a tunneled shoreline crossing, and a shore-based pumping station. The system is the world’s largest and deepest cold-water pipeline and has the capacity to deliver 27,000 gpm of 4 deg. C. water and over 40,000 gpm of warm water to the technology park. Makai received a national award from the American Society of Civil Engineers for this project as one of the six most outstanding CE projects in 2003.
Cornell University Lake Source Cooling
Makai was selected by Gryphon International Engineering Services and Cornell University to design a 63″ diameter HDPE intake and a 48″ diameter outfall pipeline in Cayuga Lake, NY to provide 20,000 tons of centralized cooling for the university.
More Info
The intake pipeline is two miles long with an intake at 250′ depth. The pipeline provides 32,000 gpm of cold water and has a 75-year lifetime. Construction was completed in 1999. The system has been operating since 2000 and has cut electricity needed for air conditioning by 87%.
Indian OTEC Pipeline
In 1998, Makai provided conceptual designs and design guidance for an OTEC intake pipeline and mooring system in India.
More Info
Makai was contracted by the National Institute of Ocean Technology (NIOT) in Madras, India, for the conceptual design of the deep water intake pipeline, the effluent pipeline, and the mooring system for an experimental floating OTEC Plant. The analysis included dynamic modeling of pipe bending, shown at right.
The NIOT OTEC barge is scheduled to be 72 meters long and will be supplied 1415 kg/s of deep cold seawater through a 1 meter diameter pipeline from a minimum depth of 1000 meters. The mooring is 1220 meters deep.
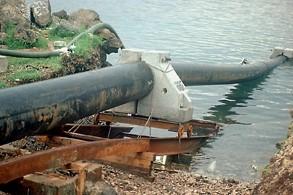
Four Outfalls in American Samoa
In 1991 and 1996, Makai designed four outfall pipelines in American Samoa, including the Tafuna, Utulei, Aunu’u, and Pago Pago outfalls.
More Info
Tafuna Outfall: This polyethylene pipeline installed in 1996, is 24″ in diameter, 1500′ in length and extends from the shoreline to a depth of 95′. The pipeline is anchored along its entire length for protection against frequent hurricanes and the large waves and strong currents that accompany them. The anchoring systems used were a combination of rock bolts and Manta Ray sand embedment anchors.
Utulei Outfall: This was a very challenging pipeline design and installation because of the extreme slope that existed along the course of the pipeline. The outfall pipeline is 24″ in diameter, 350′ in length, and it begins at the reef edge at a depth of 5′ and plunges to a depth of 165′. The pipeline has a free floating catenary section that spans the steep slope, and it is heavily anchored at the bottom in deep water.
Aunu’u Outfall: This is a 6″ outfall, 400′ in length, designed to serve a small community of approximately 400 people. It is installed across a heavily exposed reef flat which is subject to high waves and currents. The pipeline is partially buried and is anchored to the reef with rock bolts.
Pago Pago: In 1991, Makai designed and managed the construction of a long, medium depth outfall in Pago Pago Harbor, American Samoa. This 16″ polyethylene pipeline is 8500′ long and discharges near the mouth of the harbor at 176′ depth. It carries waste water from the Starkist Samoa and the Samoa Packing Tuna Canneries. The pipeline was installed using the controlled submergence techniques and was accurately laid on a curved route along the edge of the harbor. Concrete covers were designed to protect the pipeline at isolated locations from ship anchors and harbor traffic. The lifetime of the pipeline was maximized by minimizing the use of exposed metallic parts in the underwater construction. The pipeline was designed and installed in a short period and was completed ahead of schedule and well under budget.
NELHA 40″ Cold Ocean Water Intake Pipeline
In 1987, a project funded by the State of Hawaii and the U.S. Department of Energy, Makai designed a 40″ polyethylene cold water pipe to be used jointly by the Natural Energy Laboratory and the Hawaii Ocean Science and Technology (HOST) Park sites on the Big Island. At the time of construction, it was the largest deep-water intake pipeline in the world.
More Info
This pipe is a larger and more rugged version of the previous MOE 12″ pipe design at NELHA and includes a 3000′ long buoyant section. Makai assisted in the deployment of this pipe to a depth of 2200′ in August 1987.
NELHA 18″ Cold Water Pipeline
In 1987, Makai designed and provided construction management for an 18″ down-the-slope cold water intake at the Natural Energy Laboratory of Hawaii.
More Info
The goal was to install a reliable, minimal cost, deep-water intake system to 2000′. This polyethylene design differs from previous NELHA pipelines in that the deep water pipe is buoyed approximately 40′ off the bottom on a series of pendants, the deployment was accomplished without major offshore equipment. This pipeline was successfully deployed in October, 1987, and is still operational.
OTEC Pipeline Research
In 1984 Makai was responsible for the concept development, design and deployment planning for an 8′ diameter down-the-slope OTEC pipe test.
More Info
Working under a subcontract to Hawaiian Dredging and Construction, on a NOAA/DOE program, Makai was responsible for the concept development, design and deployment planning for an 8′ diameter down-the-slope OTEC pipe test. Part of the test was the demonstration of diver-free installation techniques suitable for very deep, large diameter pipelines on the steep, 42 degree slope. The concept included a flexible pipe joint that conformed to the bathymetry. Pipe deployment was successfully accomplished as planned using heavy lift barges and closed-circuit underwater television. The design included instrumentation for the measurement of hydrodynamic loads on the pipe after installation. Makai subsequently analyzed the hydrodynamic data from this test project.
Long Operating OTEC Pipeline
In 1981, Makai conceived, designed and managed the construction of an experimental, polyethylene OTEC pipeline, 12″ in diameter, for the State of Hawaii.
More Info
This one-mile long pipeline has an intake at 2000′ and utilizes a unique 3000′ long free-floating catenary section to avoid contact with the steep, rocky bottom. The pipeline was installed in 1981 off Keahole Point, Hawaii. In spite of its “temporary” design life of 2 years, it has survived many major storms including a hurricane and was operational for over twelve years.
Mini OTEC
In 1979 Makai engineered several portions of the Mini-OTEC project under contract to Dillingham Corp. This was a full OTEC system demonstration.
More Info
This project was a full demonstration of Ocean Thermal Energy Conversion (OTEC) and jointly funded by the State of Hawaii, Lockheed, Dillingham and Alfa Laval. Makai designed a 2′ diameter polyethylene pipe that served not only as an intake pipe from a 2000′ depth, but also as the “mooring line” for the 120′ x 35′ barge. The initial design for the barge layout, seawater intakes (cold and warm), effluent lines, and pumps was also done by Makai. Makai developed and planned the deployment scheme and participated in the at¬sea deployment. On August 2, 1979, Mini¬OTEC produced 50 kW of power and consumed 40 kW, for a net positive output of 10 kW. This was the first time that a positive output had been achieved from any OTEC facility. In 1980, the National Society of Professional Engineers awarded Mini-OTEC as being one of the ten outstanding engineering achievements in the United States that year.
Interested in Makai’s Marine Pipeline Services?
ReACH OUT!
Contact us by sending in this form any time you need professional support or have any questions. You can also fill in the form to leave your comments or feedback for Makai’s team.